Two companies developing robotic fruit harvesters returned to West Coast orchards in 2023, and by grower accounts they have improved their game.
Tevel of Israel and the San Francisco Bay Area’s advanced.farm returned to California and Washington orchards to pick stone fruit and apples. Growers who hosted them say they have made strides in efficiency and accuracy but still have a way to go before commercialization.
“They’re getting there,” said Rob Blakey of Stemilt Growers, who watched both Tevel and advanced.farm in the fall.
Washington’s tree fruit industry has set a conservative goal of between five and 10 years before growers can purchase or hire a robotic harvester to pick apples for between 2 and 3 cents each, according to the Washington Tree Fruit Research Commission.
Tech companies have their own timelines and approaches.
Tevel makes an automated harvester with suction-cup-equipped drones tethered to a bin filler with a series of delivery belts mounted on an orchard platform. Advanced.farm’s harvester is a self-driving vehicle with six arms, also with suction-cup end effectors, that moves fruit from trees to a system of conveyors that feed a bin filler.
Fresh Fruit Robotics of Israel, which uses fingered grippers as end effectors, has a few years of Washington orchard trials under its belt but worked only in Israeli orchards in 2023, said founder Avi Kahani.
Tevel
Tevel worked in Washington and California orchards for the second year but has more history in Israel and Italy, where the company expects to commercialize first, said Ittai Marom, U.S. general manager of Tevel. The company declined to estimate a specific timeline.
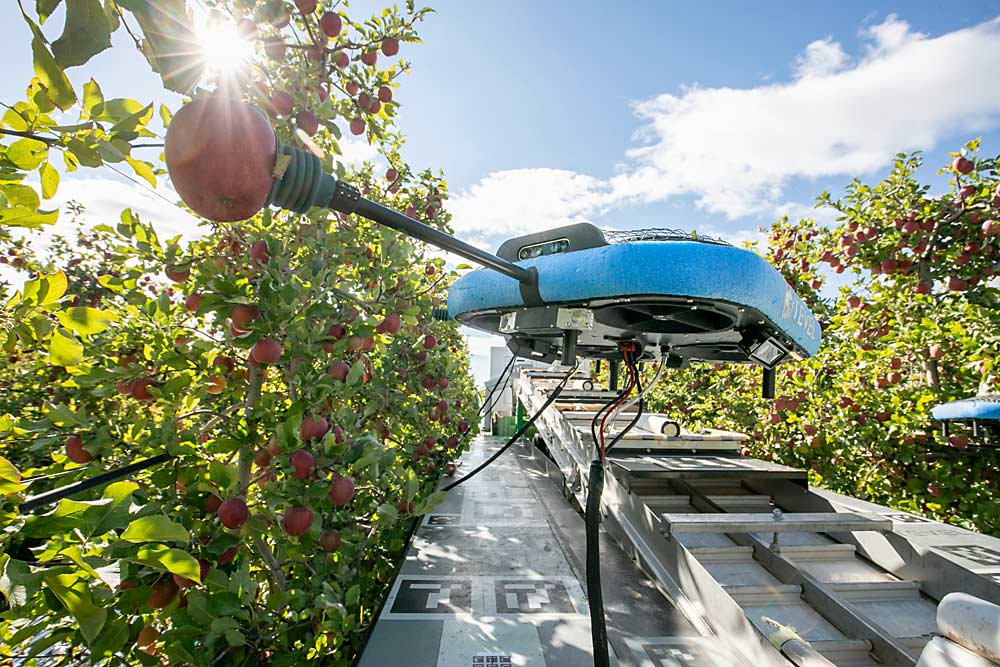
“Once we reach that milestone in Europe, the U.S. and South America will follow,” Marom said.
During the past year, Tevel mounted its robotic picking kit onto the Alpha 1 orchard platform made by California’s S&S Metal Fabrication. Collectively, the machine is named Alpha-Bot.
Tevel held invite-only demos for select growers in 2022, but in 2023 it allowed Good Fruit Grower to watch the Alpha-Bot work near Quincy, Washington.
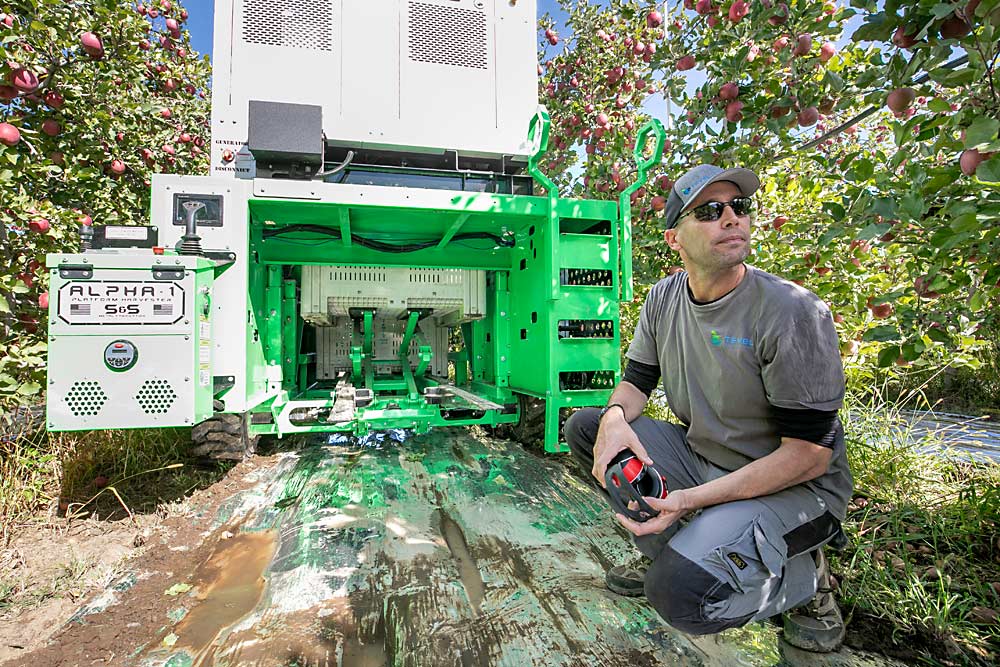
With a high-pitched whir, the camera-equipped drones hovered and studied the canopy to select and pick apples, then dropped them onto a padded belt that delivered the fruit to a bin filler carried by the platform. Occasionally, two drones bumped into each other, momentarily buzzed a little louder, corrected course and resumed work. That’s part of the design, as each drone tries to maximize its range, Marom said.
Sometimes, the drones successfully picked on the first try. Other times, they needed a few attempts. Still others, they gave up on a particular apple and moved on.
“We don’t want it wasting too much time on a single piece of fruit,” Marom said.
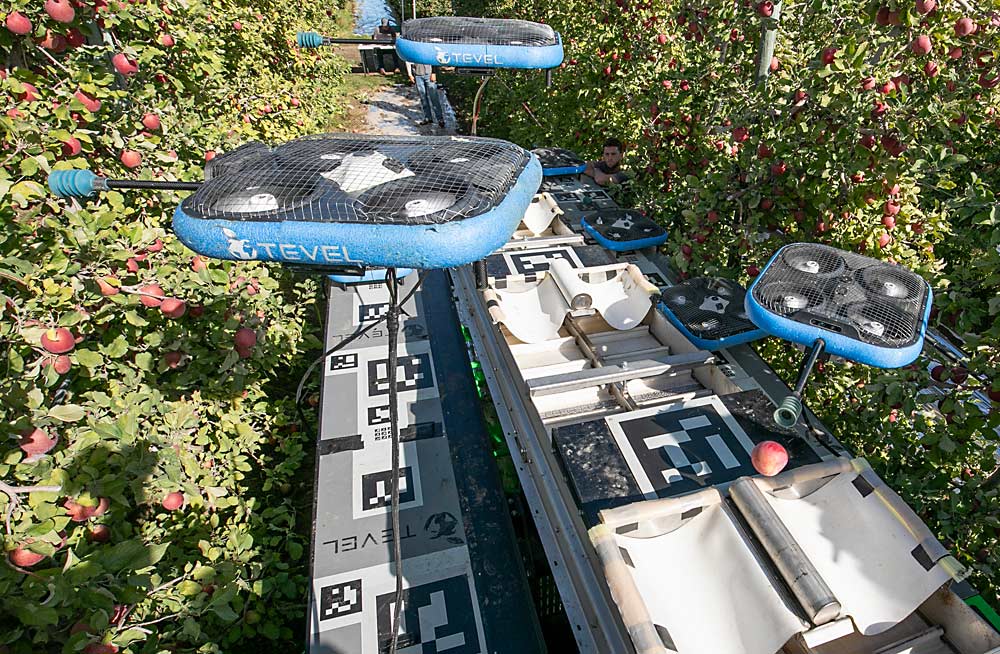
Whether the machine picks or not, the computer records each apple and gives it a unique identification number, later generating a histogram of weight, color and diameter. The computer system operates locally but can be connected to the cloud.
Tevel harvested at two U.S. farms in 2023: a stone fruit producer in California and Stemilt Orchards in Washington. The Washington trials were backed by a $25,000 out-of-cycle grant from the Washington Tree Fruit Research Commission to reimburse Stemilt for hosting the trials.
Tevel also performed trials in Italy and Chile. At each place, the farms set aside the fruit picked by the machine for independent quality comparisons.
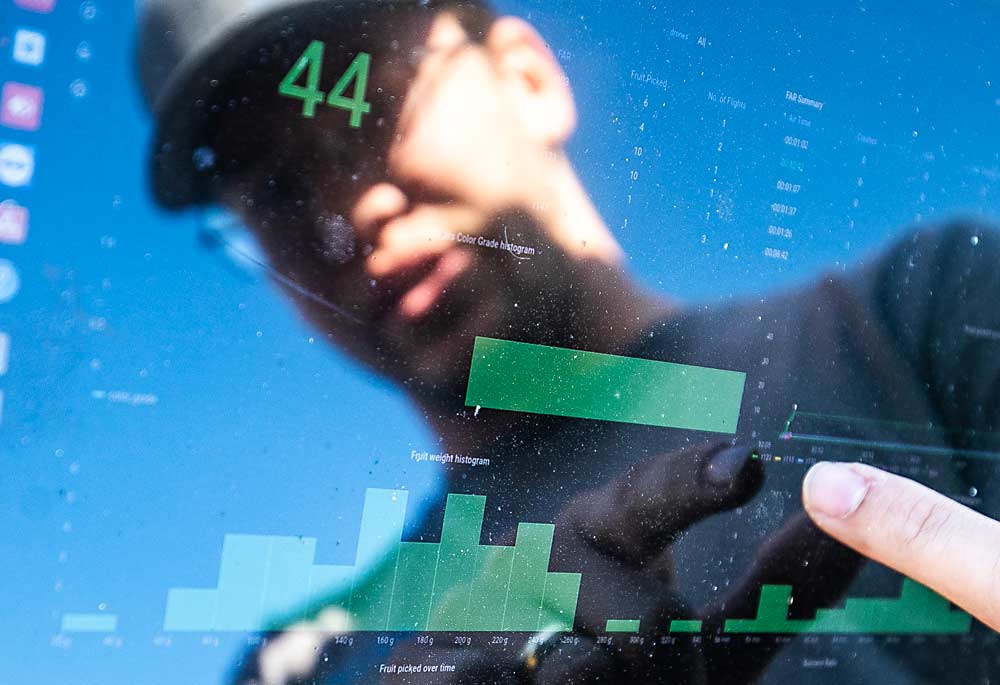
The company declined to share speed and quality data, but Marom did comment on bruising. “Globally, our robotic pickers have proven that they do not bruise the fruit more than the human pickers. As a matter of fact, in some cases, we are even better,” he said.
Currently, someone must drive the platform, though self-driving will likely be a future iteration, Marom said. In the end, one person would be able to operate four or five machines at one time.
The company is still discussing whether it will sell the machines directly, charge a service fee or offer a hybrid of both options, Marom said.
In 2023, the bot ran trials only on vertical trellises, but the company is aiming to harvest V-trellises in the future.
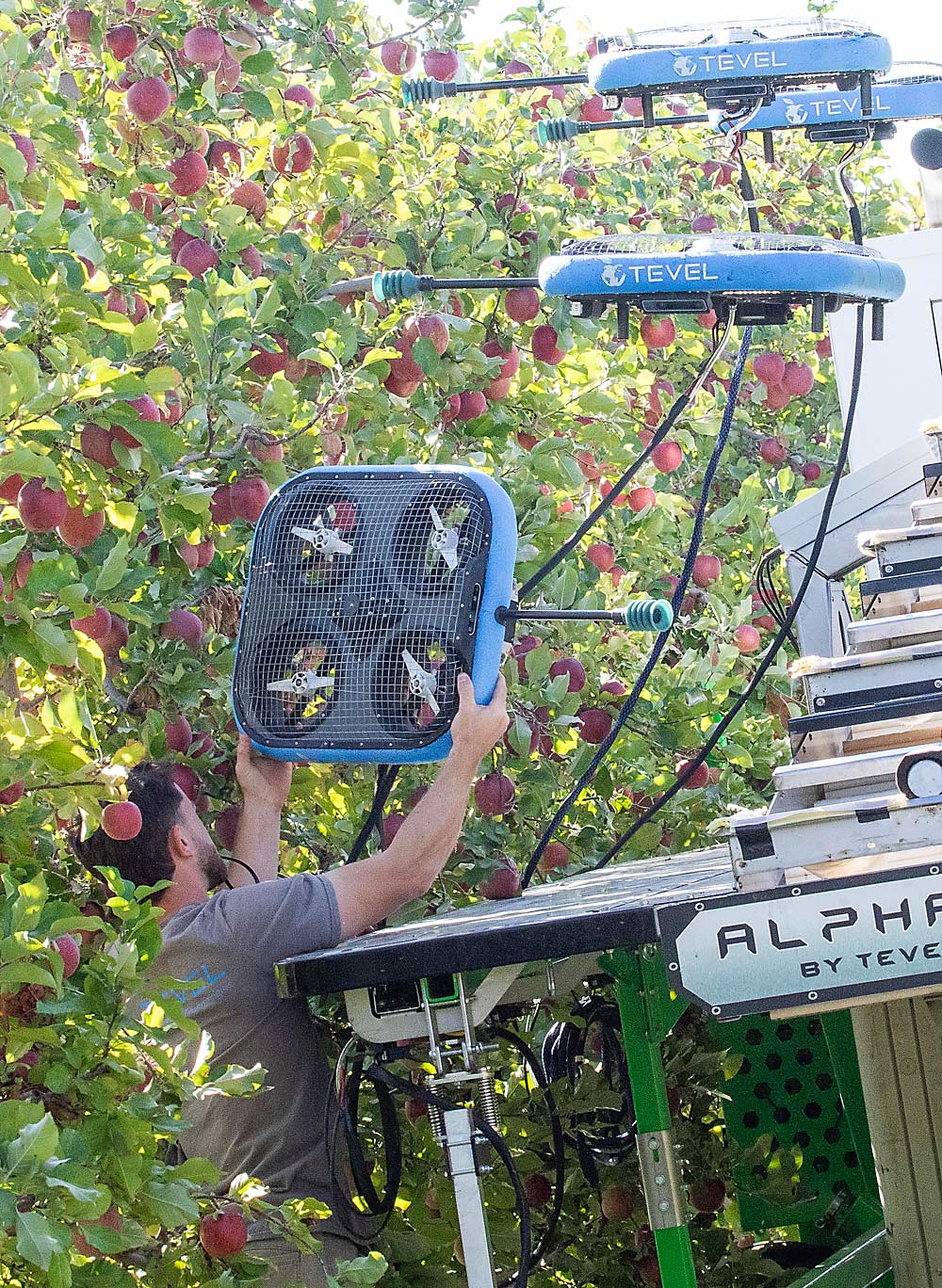
Advanced.farm
Advanced.farm’s robots — they brought two to Washington — visited seven different farms in 2023 with a prototype that resembled the one used the previous year.
“Our biggest improvement so far, and kind of what our focus was, was our speed of picking,” said Peter Ferguson, director of business development.
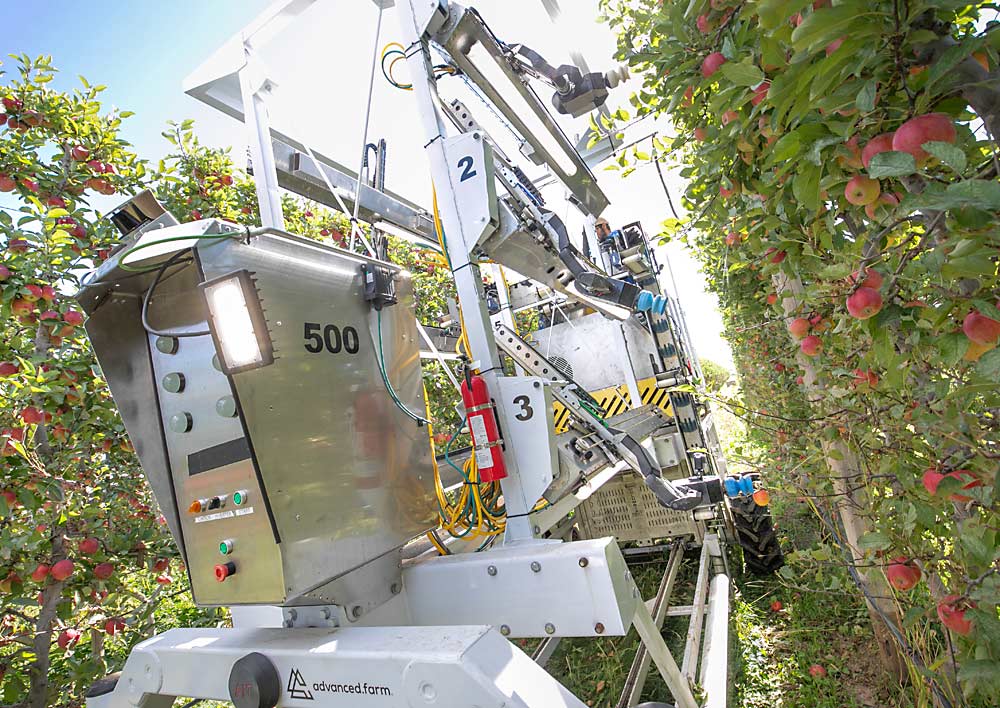
The engineering team more than doubled its pace, averaging 1,000 apples per hour. At peak times, they topped 2,500 per hour. A bin holds roughly 1,800 to 2,000 apples.
The team also modified its bin filler and conveyor belts to be gentler. In 2022, they damaged more than half the Galas they picked; in 2023, they reduced that to less than 10 percent, Ferguson said.
Also, they encased the suction cup end effectors in protective plastic shells and tested thicker materials to cut down on rips. Both should reduce maintenance downtime.
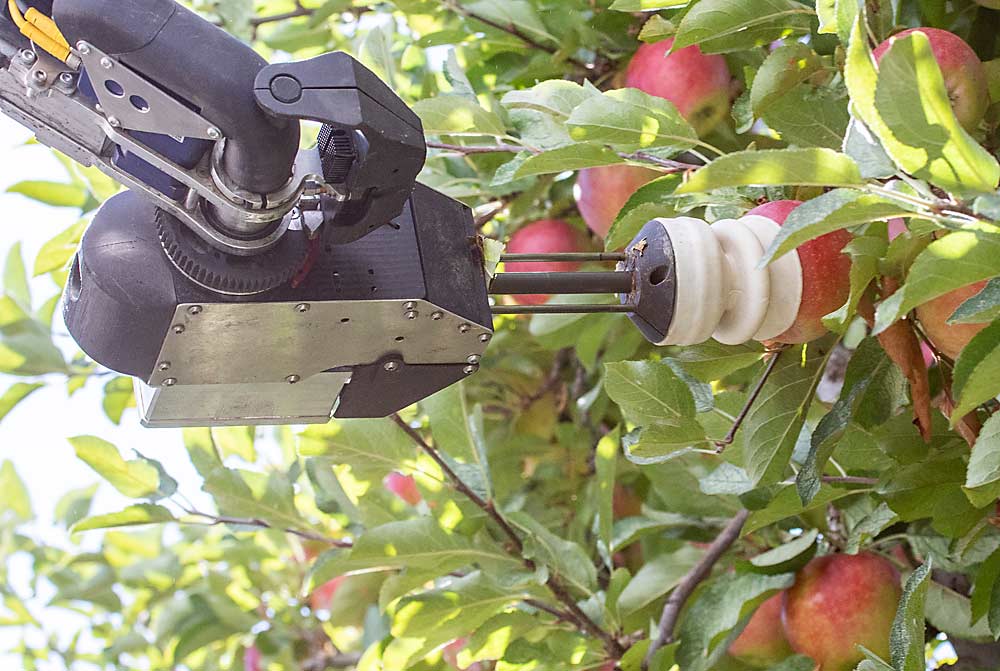
Currently, the engineers are designing for vertical trellises, with an eye toward V-trellis in the future.
Advanced.farm also scored some hefty financial backing in 2023. In October, farm equipment giant CNH Industrial announced a minority investment in the startup.
Ferguson said the company expects to begin commercialization in 2026, after two more years of research and development. The long-term plan is to sell machines directly to growers, but the company may start with some service options to ease into the market.
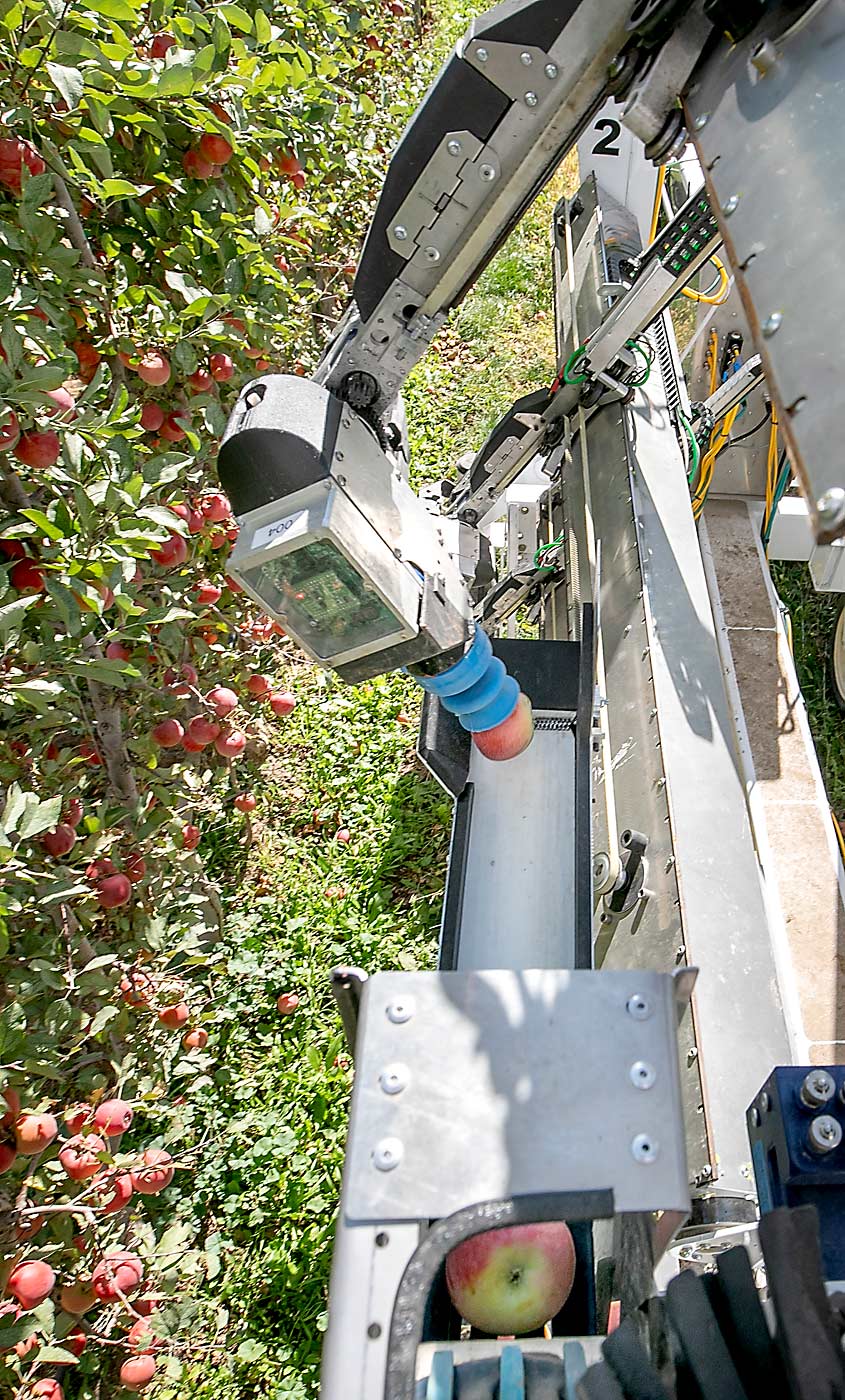
Growers pleased with progress
Growers lauded the improvements of both companies.
Both companies performed well at HMC Farms, a vertically integrated stone fruit producer in Kingsburg, California, said Drew Ketelsen, production manager. Both machines pick at night, something he likes because stone fruit handles better when it’s cool.
He especially liked Tevel’s platform mount. The green S&S platform is common in Central California stone fruit orchards for pruning, thinning and harvest. His company has several.
During the course of the 2023 harvest in Washington, the advanced.farm engineers ramped up picking speed, improved color selection and reduced bruising, said Steve Caudill, chief technical officer for Columbia Fruit Packers.
“They made huge strides in fruit handling, speed, accuracy of coverage,” he said.
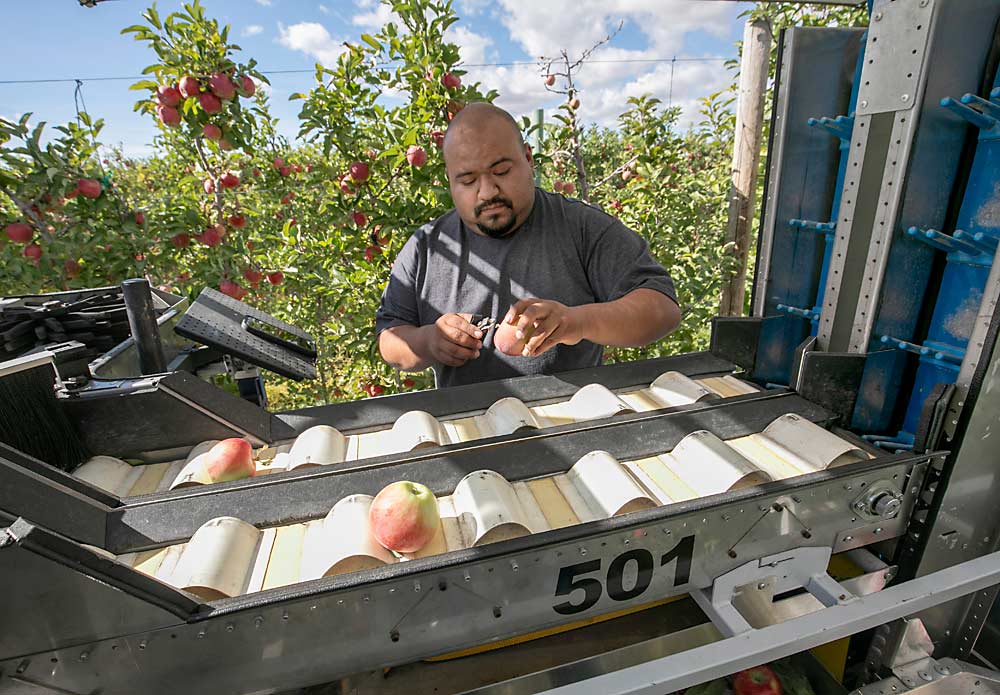
Caudill also was pleased with how the operators and engineers communicated with farm supervisors, something that doesn’t always happen with ag tech startups. Relatively new to tree fruit, Caudill spent six years at CNH Industrial building farm and fleet management software packages in Chicago. Some programmers never set foot in a field, he said.
Blakey of Stemilt also lauded recent communication between growers and startups, which are better aligning with the realities and complexities of orchards.
A robot will always prefer a simple two-dimensional system with single apples not obstructed by foliage. Though orchardists have spent decades moving in that direction, most blocks are not set up that way.
The goal is getting the machine to pick enough fruit in a timely manner at a cost relative to manual harvest — a complex goal, Blakey said.
“We need to be patient with them.”
—by Ross Courtney
Robot panel: Automated pickers highlight tech session at Hort Show
A robotic harvest panel, which also featured a pear robot developer, attracted a curious crowd during the technology session at the Washington State Tree Fruit Association Annual Meeting in December in Kennewick.
“My phone’s blowing up with questions,” said Keith Veselka, a Central Washington grower who moderated the four-person panel.
Representatives from advanced.farm and Tevel, two companies that ran trials in Washington and California in 2023, participated. So did JJ Dagorret of Automated Ag Systems, a Moses Lake, Washington, company that makes the Bandit Cyclone, a harvest-assist platform that uses vacuum-powered tubes attached to picker bags.
The newest guy on the block — for the Washington audience — was Peter Frans de Jong of the Wageningen University in the Netherlands, where he leads a team working on a pear robot. As far as the panelists knew, they were the only ones trying that.
Unlike in the United States, most pears are trellised in the Netherlands, he said.
“Picking pears is a little bit more complicated even than picking apples,” de Jong said. With apples, the picking movement is usually a twist and pull. Pears require an upward swing, which risks damaging the tree branches above with the hardware of the arm’s end effector, he said. The team held field trials in fall 2023.
“It’s still very slow, but it does the job,” he said.
—R. Courtney
How do I purchase a harvesting robot.
I would email the companies to inquire, but these machines aren’t quite for sale at a retail level yet. They’re still working out the bugs and at least one of them is planning a service business model, not direct sales. At least, that was the case last I wrote about them.